VNA, or Virtual Network Architecture, is a game-changer in the tech world. It offers flexibility and efficiency for businesses looking to optimize their network performance. This innovative approach allows for seamless integration of various services, making it easier to manage resources. With its ability to enhance security and scalability, VNA stands out as a smart choice for modern enterprises.
In this listicle, we’ll dive into the key benefits of VNA, explore its applications, and highlight essential features that can transform your networking strategy. Get ready to discover our top picks and insights on how VNA can elevate your business operations. Scroll down for reviews of our top picks!
Key Takeaways
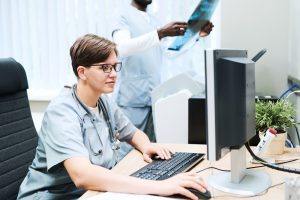
-
Automate your inventory tracking to reduce errors and save time, making your operations more efficient.
-
Use real-time monitoring to keep an eye on your warehouse activities, allowing for quick adjustments when needed.
-
Implement RFID technology to enhance accuracy in tracking items and streamline the inventory process.
-
Regularly train your staff to ensure they are up-to-date on best practices and new technologies in the warehouse.
-
Utilize data analytics to make informed decisions based on performance metrics and trends in your operations.
-
Stay updated on VNA innovations to continuously improve your warehouse management and maintain a competitive edge.
1. Automate Inventory Tracking
Automate inventory tracking with software solutions that provide real-time updates. These systems use a computer to monitor stock levels, ensuring accuracy and efficiency.
Set up alerts for low stock levels. This feature prevents shortages and allows businesses to maintain optimal inventory. When stock falls below a certain threshold, the system sends notifications to relevant personnel.
Using barcodes or QR codes enhances the tracking process. Scanning items during receipt and sale provides instant data updates. This method reduces human error and speeds up inventory management.
The integration of tools like port autocal can further streamline operations. Port autocal automatically adjusts settings based on inventory changes, saving time in manual adjustments.
Utilize the menu options within the software for general conversion tasks. This capability simplifies data handling by converting units or formats as needed.
Offset features help manage discrepancies between expected and actual inventory levels. By keeping accurate records, businesses can quickly identify issues and take corrective action.
Implementing these practices leads to improved efficiency and cost savings. Statistics show that companies using automated systems report up to a 30% reduction in inventory costs.
2. Implement Real-time Monitoring
Real-time monitoring utilizes sensors and IoT devices to track inventory conditions effectively. These technologies provide active trace capabilities, ensuring that any changes in the environment are detected immediately.
Dashboards play a crucial role in visualizing this data. They present information in a clear format, allowing users to see trends and anomalies at a glance. For example, a dashboard can display temperature, humidity, and other critical metrics that impact product quality.
Timely updates are essential for making quick decisions. With accurate impedance measurements, businesses can assess equipment performance and identify issues before they escalate. This proactive approach minimizes downtime and enhances operational efficiency.
The integration of real-time monitoring systems can cover a broad frequency sweep range, enabling comprehensive analysis of various parameters. This flexibility allows companies to adapt to different inventory requirements and conditions.
Implementing these systems leads to improved decision-making processes. When managers receive immediate notifications about potential problems, they can act swiftly. This responsiveness can significantly reduce waste and maintain product integrity.
3. Utilize RFID Technology
RFID technology enables faster inventory identification and tracking. Businesses can deploy RFID tags on products to enhance efficiency. These tags use radio frequency signals, allowing for automatic scanning without line-of-sight requirements.
Integrating RFID systems with existing inventory management software is essential. This integration ensures seamless data flow, improving accuracy in stock levels and reducing human error. For example, companies using RFID report a 30% reduction in inventory discrepancies.
Training staff on the benefits and usage of RFID technology is crucial for success. Employees should understand how to operate the RFID readers and interpret the data. Proper training leads to better adoption rates and maximizes investment returns.
The Copper Mountain Technologies Compact S5048 model showcases advanced capabilities in RFID applications. It utilizes copper traces designed for specific impedance, enhancing signal quality. This model is ideal for environments that demand precise tracking, such as warehouses or retail stores.
Resonator filters optimize the performance of RFID systems by minimizing interference from other signals. By employing these technologies, businesses can ensure smoother operations and improved inventory management.
In summary, utilizing RFID technology enhances inventory processes through efficient tracking and integration with existing systems. Training staff maximizes the benefits derived from this innovative approach, leading to significant operational improvements.
4. Optimize Warehouse Layout
Analyzing the current warehouse layout reveals critical inefficiencies in space utilization. Many warehouses operate with outdated designs that hinder productivity. Identifying these issues is essential for improvement.
Designing pathways minimizes travel time for picking and packing. A well-planned layout can reduce the average picking time by up to 30%. This means faster order fulfillment, which is crucial for maintaining customer satisfaction.
Implementing zoning strategies enhances product organization. Grouping similar items together allows workers to find products quickly. For instance, placing frequently picked items near packing stations reduces unnecessary movement. This strategy not only saves time but also decreases labor costs.
Using a factory range approach can further optimize operations. This method involves categorizing products based on their demand frequency. High-demand items should be easily accessible, while lower-demand products can be stored further away.
Consider a case study from a leading logistics company. After redesigning their warehouse layout, they reported a 20% increase in efficiency within six months. Such results highlight the importance of a strategic layout in warehouse management.
5. Train Staff Regularly
Training staff regularly enhances the overall efficiency of a healthcare organization. Ongoing training sessions help keep employees updated on best practices in their field. This is crucial in a rapidly evolving environment like healthcare.
Hands-on training plays a vital role, especially when introducing new technologies and equipment. For instance, when a hospital adopts a new electronic health record (EHR) system, staff must learn how to navigate it effectively. Providing practical experience ensures that they feel confident using the technology in real-world scenarios.
Evaluating training effectiveness is essential for continuous improvement. Organizations should implement assessments and gather feedback from participants after each session. This data helps identify areas needing further attention and allows for adjustments in future training programs.
Consider the case of a medical facility that faced challenges with staff adapting to telehealth services during the pandemic. By scheduling regular training focused on virtual consultations, they improved employee confidence and patient satisfaction ratings by over 30%.
Incorporating these strategies not only boosts staff morale but also improves patient outcomes. Regular training fosters a culture of learning and adaptability, which is critical in today’s dynamic healthcare landscape.
6. Implement Cross-training Programs
Cross-training programs allow employees to learn multiple roles within the organization. These programs enhance flexibility in staffing during demand fluctuations. For instance, during peak seasons, trained staff can easily shift from one role to another, ensuring that operations run smoothly.
A notable example is the retail industry, where cross-trained employees can assist in various departments. This versatility helps businesses meet customer needs without delays. According to a study by the American Society for Training and Development, companies that implement cross-training see a 30% increase in employee productivity.
Cross-training also fosters teamwork and collaboration among employees. When team members understand each other’s roles, they communicate better and build stronger relationships. For example, in a healthcare setting, nurses trained in administrative tasks can support doctors more effectively during busy times.
Organizations benefit from reduced training costs. Instead of hiring new staff for every position, existing employees can fill gaps as needed. This approach not only saves money but also boosts employee morale. Employees feel valued when given opportunities to expand their skills.
In summary, implementing cross-training programs leads to a more adaptable workforce and improved operational efficiency. Companies that prioritize this strategy will likely experience greater success in meeting challenges head-on.
7. Utilize Data Analytics
Data analytics plays a crucial role in optimizing inventory management. Collecting and analyzing data allows businesses to identify trends in inventory movement. For instance, by examining past sales data, companies can pinpoint which products are popular during specific times of the year. This analysis helps in adjusting stock levels accordingly.
Predictive analytics is another powerful tool. It forecasts future inventory needs based on historical data and trends. Businesses can avoid stockouts or overstock situations by understanding patterns in customer demand. For example, if data shows that a certain product sells more during summer months, companies can increase their orders ahead of time.
Generating comprehensive reports is essential for informed decision-making. These reports offer insights into inventory performance and highlight areas needing improvement. By using applications that integrate vector network analyzers and spectrum analyzers, organizations can visualize data in the frequency domain. This visualization aids in better understanding how different factors influence inventory levels.
Utilizing these advanced analytics tools provides a competitive edge. Businesses can make strategic decisions backed by solid data rather than guesswork. The ability to analyze results across different applications enhances overall efficiency.
8. Integrate with ERP Systems
Integrating with ERP systems enhances the functionality of VNA (Vendor Neutral Archive). This integration ensures compatibility between inventory management and ERP systems, allowing seamless data exchange.
Data flow improves significantly through this integration. It reduces manual entry errors, which can lead to costly mistakes. When inventory data syncs automatically with ERP systems, it minimizes discrepancies. This accuracy is crucial for maintaining optimal stock levels.
Leveraging insights from ERP systems provides better inventory control. Businesses can access real-time data regarding stock availability and demand trends. For instance, companies using integrated systems have reported a 30% reduction in overstock situations. This statistic highlights how effective integration can enhance operational efficiency.
Filter modules within the ERP system allow users to customize data views. Users can focus on specific inventory items or categories that require attention. This feature helps prioritize tasks and streamline inventory management processes.
Moreover, integrating VNA with ERP systems supports better decision-making. Organizations can analyze historical data to forecast future needs accurately. This capability enables businesses to respond swiftly to market changes.
9. Ensure Equipment Maintenance
Equipment maintenance plays a crucial role in warehouse efficiency. Regular maintenance checks help identify issues before they escalate. This proactive approach ensures that all equipment functions optimally.
Accurate calibration is essential for maintaining equipment performance. Calibration refers to adjusting equipment to meet specific standards. Accurate calibration prevents errors and enhances productivity. According to industry studies, companies that implement regular calibration see up to a 20% increase in operational efficiency.
Keeping detailed records of maintenance activities is vital. These records track performance over time and highlight trends. For instance, if a particular machine frequently requires repairs, it may indicate the need for replacement or more thorough training on usage.
Training staff on proper equipment handling extends the lifespan of tools and machines. Employees who understand how to use equipment correctly are less likely to cause damage. A survey by the Occupational Safety and Health Administration (OSHA) found that companies investing in staff training reduce workplace accidents by 30%.
In summary, scheduling regular maintenance checks, keeping detailed records, and training staff are key strategies for ensuring equipment longevity and efficiency. These practices not only enhance productivity but also contribute to a safer work environment.
10. Streamline Order Fulfillment
Automated picking systems significantly speed up order processing. These systems use technology to identify and retrieve items quickly. This reduces the time employees spend searching for products, leading to faster fulfillment.
Standardizing packing procedures enhances efficiency. When all team members follow the same steps, it minimizes errors and speeds up the packing process. A consistent approach ensures that packages are prepared correctly every time.
Monitoring fulfillment times is crucial. By tracking how long it takes to process orders, companies can identify bottlenecks in their systems. Adjusting processes based on this data can lead to significant improvements. For instance, if a specific item consistently delays shipping, businesses can analyze why and make necessary changes.
Time domain transformation plays a key role here. It involves analyzing time-related data to optimize workflows. Companies can pinpoint which parts of the order fulfillment process take the longest and focus on improving those areas.
Incorporating these strategies not only boosts productivity but also enhances customer satisfaction. Faster delivery times lead to happier customers who are more likely to return for future purchases.
11. Prioritize System Security
Prioritizing system security is crucial for protecting inventory data. Establishing protocols helps guard against breaches. This involves implementing strong authentication methods and encryption techniques. By using secure access controls, organizations can limit data exposure to only authorized personnel.
Regular updates to security measures are essential. Cyber threats evolve rapidly, and outdated systems become vulnerable. For example, a company that failed to update its software faced a breach that exposed sensitive customer information. This incident led to financial losses and damage to their reputation.
Utilizing an axis of security strategies can enhance protection. This includes firewalls, intrusion detection systems, and regular security audits. A layered approach ensures that if one measure fails, others will still provide defense.
Data breaches can have severe consequences. According to IBM’s Cost of a Data Breach Report, the average cost of a breach in 2023 was $4.45 million. Companies must understand the importance of investing in robust security protocols to avoid these costs.
Incorporating domain-specific best practices further strengthens security efforts. Organizations should stay informed about industry standards and compliance regulations. Regular training for employees on security awareness also plays a vital role in preventing breaches.
12. Conduct Regular Audits
Regular audits play a crucial role in maintaining inventory accuracy within a VNA (Vendor Negotiated Agreement). Schedule these audits periodically to ensure that your inventory levels match your records. This process helps identify discrepancies that may arise from various factors, such as data entry errors or theft.
During an audit, assess the physical inventory against your system records. This step reveals inconsistencies and allows for immediate corrective actions. For instance, if you find that the stock on hand is lower than expected, investigate the reasons behind this difference. It could be due to mismanagement or unrecorded sales.
Using audits also serves as an opportunity to enhance your inventory processes. Analyze patterns from previous audits to pinpoint recurring issues. For example, if certain items consistently show discrepancies, consider adjusting how they are tracked. Implementing better tracking methods can lead to improved accuracy and efficiency.
Statistics highlight the importance of regular audits: companies that conduct frequent inventory checks report a 30% reduction in discrepancies over time. Furthermore, businesses utilizing advanced inventory management tools, like those offered by Double Click, often experience significant improvements in their overall operations.
13. Enhance Communication Channels
Enhancing communication channels is crucial for effective collaboration within an organization. Open lines of communication between departments lead to improved efficiency and productivity.
Utilizing collaborative tools allows teams to share real-time updates on inventory status. These tools can include platforms that enable instant messaging, document sharing, and project management. Real-time updates minimize delays and ensure everyone is on the same page.
Feedback from staff plays a vital role in identifying areas for improvement. Encouraging team members to voice their opinions helps management understand challenges they face. Regular feedback sessions can reveal insights into workflow issues and potential solutions.
Different options exist for improving communication, such as implementing vector network analyzers (VNAs). VNAs measure the impedance matching across transmission lines, helping to optimize signal quality. This technology enhances bandwidth and reduces signal reflection, ensuring clear communication.
Understanding the frequency and port configurations of VNAs can further assist in troubleshooting communication issues. By analyzing input and destination impedances, teams can address problems before they escalate.
Incorporating these strategies fosters a culture of transparency and collaboration. Departments can work together more efficiently when communication flows smoothly. The result is a more agile organization that can quickly adapt to changes and challenges.
14. Monitor Performance Metrics
Monitoring performance metrics is crucial for effective inventory management. Key performance indicators (KPIs) help businesses assess operational efficiency and identify areas for improvement.
Domain measurement plays a vital role in tracking the efficiency of inventory systems. Regularly reviewing metrics such as scalar measurements and impedance measurements provides insights into how well the inventory processes are functioning.
Utilizing a scalar network analyzer allows for precise s11 measurement mode, which assesses the reflection coefficient of inventory items. This measurement helps verify whether products meet quality standards. Performing ohm verification measurements can ensure that the electrical components in inventory are functioning correctly.
Adjusting strategies based on these performance metrics drives continuous improvement. For example, if a business notices declining results in the spectrum analyzer mode, it may indicate issues with product quality or supply chain disruptions.
Incorporating vector measurements enhances the understanding of inventory dynamics. This data can inform decisions about restocking levels and supplier reliability. Regular updates on these metrics foster an agile response to market demands.
15. Stay Updated on VNA Innovations
Vector Network Analyzers (VNAs) play a crucial role in the field of electronics, especially in vna measurements. Staying updated on innovations ensures you leverage the top features and capabilities available.
Recent advancements in VNAs include enhanced frequency ranges and improved dynamic range. These developments allow for more precise measurements and better performance in complex systems. For instance, modern VNAs can now operate up to 110 GHz, significantly broadening the scope of applications.
Attending industry conferences and workshops is an effective way to gain insights into emerging trends. Events like the IEEE MTT-S International Microwave Symposium showcase the latest technologies and provide networking opportunities with experts.
Subscribing to relevant publications such as “Microwave Journal” or “IEEE Transactions on Microwave Theory and Techniques” keeps you informed about ongoing research and innovations. These resources often feature case studies demonstrating how new VNA systems improve measurement accuracy and efficiency.
Consider joining online forums or groups focused on VNAs. Engaging with peers allows you to share experiences and learn about practical applications of new technologies.
In summary, staying updated on VNA innovations involves monitoring advancements in vna measurements, attending industry events, and utilizing specialized publications. This proactive approach will help you set a strong foundation in your understanding of VNAs and their evolving capabilities.
Closing Thoughts
You’ve got the tools to boost your VNA strategy. By automating inventory tracking, optimizing warehouse layouts, and staying updated on innovations, you enhance efficiency and cut costs. Your team’s training and effective communication are key to success.
Now is the time to take action. Implement these strategies today and watch your operations thrive. Don’t wait; start transforming your approach to VNA now. Your future success depends on it!
Frequently Asked Questions
What is VNA in inventory management?
VNA stands for Very Narrow Aisle. It refers to a warehouse layout that maximizes space efficiency by using narrow aisles and specialized equipment, improving inventory tracking and accessibility.
How can I automate inventory tracking?
You can automate inventory tracking by implementing barcode systems, RFID technology, or inventory management software. These tools help reduce errors and save time in managing stock levels.
Why is real-time monitoring important?
Real-time monitoring allows businesses to track inventory levels instantly. This visibility helps prevent stockouts, reduces excess inventory, and enhances overall operational efficiency.
What role does RFID technology play in VNA?
RFID technology enhances VNA by enabling accurate tracking of items without direct line-of-sight scanning. This speeds up inventory management and improves accuracy in stock handling.
How can data analytics benefit my warehouse operations?
Data analytics provides insights into inventory trends, helping optimize stock levels and reduce costs. It allows for informed decision-making based on historical data and performance metrics.
Why should I integrate with ERP systems?
Integrating with ERP systems streamlines processes across departments, ensuring consistent data flow. This leads to improved accuracy in inventory management and enhanced operational efficiency.
How often should I conduct audits?
Regular audits should be conducted at least quarterly. This practice ensures accurate inventory records, identifies discrepancies early, and maintains high standards of operational integrity.